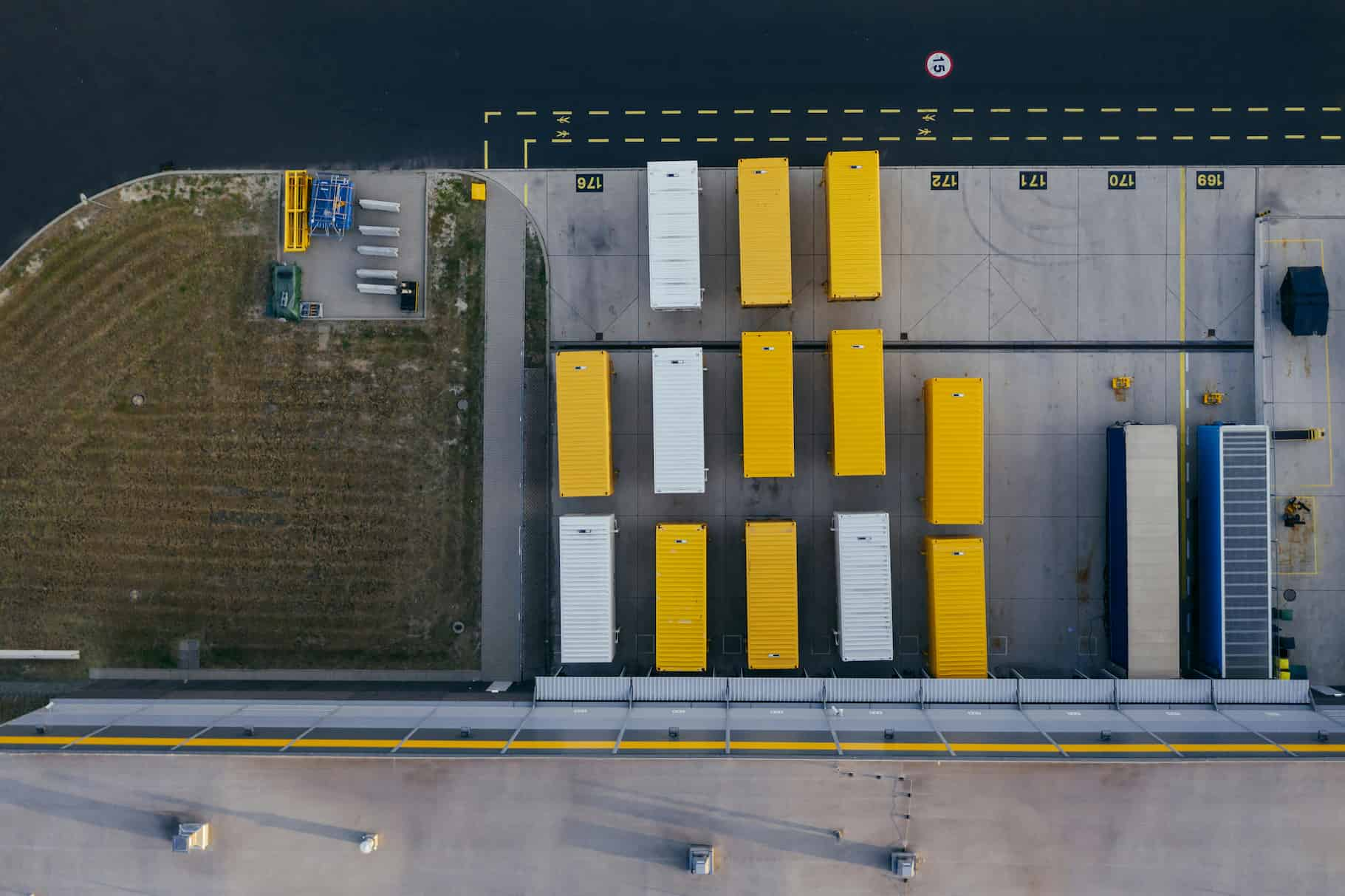
Forget everything you knew about warehouse operations. It’s 2025, and warehouse logistics are evolving faster than anything. So, to compete with emerging trends, I will reveal all the secrets to change how you manage operations within your warehouse. This guide here will give you an unparalleled edge.
Imagine starting each day knowing you’ll be buried under hundreds of phone calls, endless email chains, and messy spreadsheets. Despite your team’s best efforts, shipments are delayed, docks are backed up, and inventory sits idle. Drivers wait, carriers complain, and receiver/customer satisfaction drops.
Manual scheduling methods simply cannot keep up with the volume and speed that the modern supply chain demands. This is the nightmare warehouse managers deal with without a clean system to manage inbound and outbound traffic.
Let’s understand the problem with a little scenario: Carrier requests a pickup time (e.g., 2 PM) for unloading. Then the warehouse operator replies hours later: Sorry, 2 PM is full, can you please try 9 AM? This cycle repeats for delivery appointments (and multiplies for multi-stop loads).
This compiles to a multiple-step back-and-forth communication that wastes up to 18 hours per load. Worse? It also delays capacity sourcing because carriers won’t commit without confirmed appointments.
The biggest irony? This inefficiency hurts everyone:
- Drivers waste hours waiting
- Warehouses face unpredictable surges
- Brokers lose time managing chaos
When you think about all these problems together, scheduling might not seem like the obvious solution. But, in reality, effective dock scheduling is the solution. Dock scheduling brings structure to the chaos, improves communication across teams, optimizes dock usage, and ensures shipments move on time.
In this guide, we’ll walk you through everything you need to know about dock scheduling, why it matters, how it works, and how it can transform your daily operations.
Key Takeaways
- What is Dock Appointment scheduling?
- Who needs dock scheduling?
- Problems Vs. Impact of Dock Scheduling for Carrier and Shippers
- Benefits of Scheduling Warehouse Appointments
- What is Dock Scheduling Software?
- How to implement Dock Scheduling software for the Warehouse?
- Three Main benefits of upgrading to dock scheduling
- Tips and tricks for Scheduling Docks
- Use Case of Dock Scheduling.
What is Dock Appointment Scheduling?
Imagine not having to call carriers every time to confirm shipment or handle urgent changes. This all can be managed simply with Dock Scheduling.
“Dock appointment scheduling allows carriers, operators, or shippers to book specific times for loading or unloading goods”.
This system is powered by intelligent software that doesn’t just do all the automation but also coordinates appointments, ensures docks are utilized on time, reduces wait times, and improves overall workflows of moving goods.
Did You Know?
✓ At FreightWaves’ 3PL Summit, industry leaders noted that “controlling appointment selection” through digital dock scheduling is a “hidden profitability lever” for 3PLs warehouses because it ensures they can lock in the best time slots, execute more loads, and boost revenue per stop.
✓ Using dock scheduling software makes your dock area run much more efficiently. A fact from DatexCorp shows that with better planning and organization, you could see productivity increase by as much as 50%.
✓ According to the survey by Bluesmart, automatic scheduling has made delivery times shorter. Over 95% of customers say that getting delivery on time has increased trust and happiness in partnerships.
Who Needs Dock Scheduling?
If you own a warehouse or work with carriers or shippers, then yes, you need dock scheduling. Managing the flow of goods for the loading dock is important in almost every sector. Here’s a look at some industries where scheduling dock appointments can make a big difference.
1. Manufacturing Industry:
Most of the manufacturing industries we have seen are using the Just in Time (JIT) production model (means ordering parts or machines when they are needed just in time) for scheduling. When raw parts and materials do not arrive on time or in the correct order, which is obvious due to many challenges, it can cause significant disruptions for the production line.
Adding an efficient dock scheduling system with JIT workflows can give manufacturers real-time visibility into outbound shipments or even incoming materials. Whether you are in the food, beverage, or automotive industry, all the paper processes, collected materials, and coordinated deliveries can prevent congestion at the docks, support smoother production of goods, and reduce downtimes that cost you a lot.
2. Retail Industry:
Retailers were among the first industries to adopt dock appointment processes, setting up the tight schedules to keep inventory flowing. According to Veronica Robotics, 87% of warehouses in e-commerce and retail are planning to implement smarter scheduling in the upcoming 12 months.
The retail industry still needs more intelligent systems to handle fast-moving logistics every day. Dock scheduling provides smarter tools that cut down on administrative time, deliver real-time visibility into key performance indicators (KPIs), and support more accurate reporting on on-time arrivals and unloading times.
3. Grocery Food Chains/Wholesalers:
In a grocery warehouse, timing is everything; deliveries must happen quickly to keep products fresh and move onto the shelves without any delays.
The most important challenge all retailers share is that shipments must arrive as scheduled, products are accurate, and orders are stocked and moved within the right timeframe, while also continuously managing product shelf life to avoid waste.
Handling all of this manually can be extremely difficult and prone to errors. To address these challenges, many retailers are focusing on upgrading their store and warehouse technology.
In fact, a survey by Autostore Systems found that 81% of grocery executives believe that investing in advanced technology is essential for driving growth.
Using advanced dock scheduling tools that consider everything from estimated delivery dates to SKU-level details helps ensure goods arrive exactly when and where they’re needed while keeping dock operations balanced.
3. Transportation and 3PL Logistics Providers:
Third-party logistics companies (3PLs) face a balancing act while managing numerous clients in one facility: They have to meet strict service levels for clientele while managing top profits.
Online dock appointment scheduling systems can help 3PLs in:
- Reducing driver waiting time
- Decreasing labour costs and working hours
- Handling KPIs and monitoring success (ETAs, late times)
Jeff Kim of NTG (Frightwaves) explained that top 3PLs “store data on customer KPIs, warehouse potential needs, and dock availability” and then create a request for proposal (RFP) pricing.
4. Pharmaceutical and Healthcare Industry:
In pharmaceutical logistics, reliability is most important, as many shipments involve sensitive and high-value products that require tight control of temperature handling and timing.
A dock appointment scheduling system can help Healthcare companies ensure shipments are processed quickly, safely, and in compliance with industry regulations.
Problems Vs. Impact of Dock Scheduling for Carrier and Shippers
Warehouse Problems | Impact Created through Smart Scheduling |
Long dwell times in the warehouse (waiting, but the truck is nowhere on time) | Reduces idle time upto 45% and keeps the detention costs low with fixed appointment slots. |
Nerve-wrecking Demurrage and Detention Charges | Cuts extra fees, minimizes waiting through self-scheduling, calendar visibility reduces overlaps, and estimates each arrival time. |
Dock congestion, truck queues, slow loading, and unloading | The dock scheduling system prevents backup queues, speeds up loads by assigning docks and equipment to spread and coordinate the arrival of upcoming trucks. |
Lack of communication between the carrier, the warehouse, the shipper, and the receiver | You reduce missed shipments because of personal individual portals for tracking and communication, which have shared calendars and paperwork for everyone. |
Inefficient long labor hours eat up extra revenue | Dock appointment scheduling improves labour productivity, provides time sheets, and overtime KPIs. Keeps them in sync for all the operations from their phones. It also balances their workload ahead of time. |
Benefits of Scheduling Warehouse Appointments
What do the advantages or progress look like when these problems are fixed?
A well-managed shipping dock eliminates recurring issues. You’ll know progress is underway when clear, measurable improvements begin to show:
- Trucks get loaded faster.
- There’s a more consistent, easier-to-manage flow of trucks.
- Greater visibility into dock appointments along with easier staff planning.
- Quick access to data that measures performance and can hold carriers accountable.
- Fewer trucks idling means lower emissions and progress toward sustainability goals.
- Immediate alerts for delays or no-shows let you reassign slots and keep operations moving.
Have you noticed that front and back, we are talking about one system, particularly the dock appointment scheduling system, so what dock scheduling software actually is?
What is Dock Scheduling Software?
Dock scheduling software is a scheduling tool that helps facilities allocate time slots for trucks for loading and unloading docks. It manages when vehicles arrive and depart, preventing congestion while organizing receiving and shipping activities.
The software typically includes booking, admin scheduling, notifications, and paperless forms, and integrates with existing warehouse systems (WMS) or (TMS) to improve efficiency and reduce costs.
How to Implement Dock Scheduling Software?
If you have read this far, you must know that dock scheduling can be the heart of all logistics. But it doesn’t mean you have to just get started and start running with it. From choosing dock scheduling software to implementing one, you need careful and strategic prior planning.
1. Know Where Your Operations Stand:
Before finding the best software, you must assess your needs. Knowing where you stand helps you choose what’s best personalized for you. It also makes it super easy for you to communicate your problems in the process.
- Start by mapping exactly how trucks move through your facility today.
- Note where they queue & how long they wait.
- What keeps them from moving smoothly?
- Collect data on average wait times, peak arrival windows, and any fees you’ve paid for late or unscheduled pickups or deliveries.
This baseline gives you clear targets and helps you spot where even small tweaks will have the biggest impact.
2. Establish Clear Goals
Decide what “success” looks like for your warehouse. Whether it’s having average wait times, eliminating after-hours arrivals, or cutting detention fees by a certain percentage, take note of simple rules for booking, for example:
- How far in advance carriers must request a slot,
- What notice is required to cancel or reschedule?
- Any penalties for no-shows?
When you know the ground rules, you minimize confusion and can enforce the system fairly.
3. Choose and Configure Your Scheduling Tool
Pick a software solution that fits your operations; this might be a standalone appointment app or a dock-scheduling module in your existing TMS/WMS.
Look for features like
- A live calendar view
- Individual booking calendar for each facility
- Automated SMS/email reminders
- Easy integration with your yard-management or gate systems.
- Make sure it can handle realistic slot counts per hour based on your needs
- Built-in buffer times for unexpected delays, and clear assignments of docks or door numbers to each appointment.
- A simple booking link or portal where carriers (or their brokers) can self-schedule, reschedule, or cancel.
- Allocate your daily dock capacity into discrete time windows and assign each slot to a specific door or dock team.
- Reporting for you to measure key performance indicators
- Managing warehouse staff attendance and time reporting
- Upload and save key documents easily (BOLs, POs, images, and more) and store PDF documents securely in portals.
- Automate instant confirmations plus reminders 24 hours and a few hours before arrival. Clear visibility into who’s coming and when is the key to eliminating the “race to the dock.”
If a scheduling software facilitates all these features, you must consider it. Arrivy is the all-in-one dock scheduling platform that organizes appointments, slashes detention time, and drives greater productivity.
4. Team Training and Onboard Carriers
While choosing software, make sure you are careful and have the answer to these two questions:
- Is the software easy to understand (UI and understanding)?
- Does the software have a good response rate?
- Is there any support training provided by the software team?
- Is the pricing suitable or do they have multiple plans?
After checking all their rules, choose the best software and walk dispatchers, gate personnel, dock supervisors, and forklift operators through the new workflow.
Show admins how to read and adjust the schedule, log arrivals, and handle exceptions. At the same time, send carriers a short “how-to” guide or video tour of the booking portal and your policies.
5. Start Small, Slowly
The best technique is to utilize free trials offered by scheduling software. Start with one dock, one shift, or one key customer lane for 2–4 weeks. During this pilot, collect feedback from drivers and staff about slot lengths, buffer times, and booking windows. Track your core metrics, how much average dwell time has improved? On-time arrivals, and detention fees efficiency? Compare them against your goals. Use real-world insights to tweak settings before a full rollout.
6. Monitor, Refine, and Scale Up
Once your pilot achieves the desired improvements, expand the system to all docks, shifts, and lanes. Continue to hold regular review meetings weekly at first, then monthly, to keep an eye on key performance indicators.
Adjust slot capacities, booking rules, or staffing plans as volumes shift. Over time, this disciplined approach will keep wait times low, reduce unexpected costs, and create a predictable, efficient flow that benefits carriers, warehouse teams, and your bottom line.
The Three Main Benefits of Upgrading to Dock Scheduling
Dock scheduling software comes with numerous benefits, but the most problematic areas solved are:
Improves Long Wait Times for Carriers
When trucks arrive without a set time slot, drivers often wait in line for extended periods before they can unload or load. By assigning fixed arrival windows, we can ensure that each truck has saved some time to be processed. Carriers won’t have to circle the yard all morning; they’ll arrive just when warehouses are ready to take the next shipment.
Reduces Penalties from Late Deliveries
Late arrivals and unexpected hold-ups can incur penalty fees from customers/receivers and carriers. These extra costs raise margins and harm the warehouse’s reputation. An intelligent scheduler can improve the predictability of the arrival times of trucks.
Carriers know exactly when to show up, and warehouse staff can plan workflows so that shipments depart on time, which means avoiding a larger amount of fines.
Resource Management (Staff and Dock doors)
Without advance notice of how many trucks will arrive on any given day, it’s hard to plan staffing levels, forklift assignments, and dock equipment. Paying overtime salary and holding staff for long hours can disrupt operations. With appointment scheduling, warehouses can see the expected volume of trucks in advance.
This allows them to manage a balanced workforce, positioning the right number of forklifts, and adjusting opening hours if needed, making operations more cost-effective.
8 Key Approaches to Enhance Dock Scheduling Software Performance
Forecast demands:
Use historical data and trends to predict shipment volumes and peak times. Whenever you think about the days that get heavily packed, make sure you analyze and save slots for those appointments. This helps allocate dock doors and labor resources proactively, avoiding last-minute congestion.
Self-scheduling for carriers:
Allow carriers to book appointments online anytime. This reduces administrative burden and improves scheduling accuracy.
Scheduling system color-coding:
When you choose scheduling software, make sure it gives you the flexibility to design your booked slots on calendars. Make sure you see appointments according to different color codes made, such as Loading (red), Unloading (Yellow), Dock storage (Green), Temperature control trucks (Blue), Sensitive fragile items docks (Purple). Or can also be used to set the priority of docks. This gives your admin or scheduler a glance at where your operations are going.
Real-time updates:
Make sure you have a streamlined pipeline to get real-time updates on dock appointments and truck arrivals to quickly identify and resolve bottlenecks. Make sure everything goes in place and have complete visibility with Map view and status updates.
Automate appointment management for recurring customers:
Make sure to give access to their personalized portals so carriers, shippers, and receivers can all book appointments from one place. Automated systems can also prevent double bookings and overscheduling because everyone has the same calendar link and assigns the right docks according to availability.
Schedule buffer times:
Breaks are important, aren’t they? Or there can be unexpected circumstances! Include buffer periods between dock appointments to accommodate unexpected delays or longer unload/load times to prevent delays.
Enable dynamic scheduling:
Allow easy rescheduling and dynamic adjustment of dock appointments based on real-time conditions such as traffic delays or operational changes. Flexibility reduces downtime and frustration.
Integrate with other software and devices:
Imagine having to see everything from one dashboard. Either you use Motive for transportation tracking, or Zoho Inventory for managing warehouse products. Make sure you have the facility of not getting stuck on multiple screens, and see everything from one place.
By applying these tips and leveraging modern dock scheduling solutions, warehouses can significantly reduce wait times, prevent congestion, optimize labor and equipment use, and improve overall supply chain efficiency.
Use Case of Dock Scheduling
Carrier Appointment Booking
Use Case: A trucking company schedules a delivery time at a warehouse.
Purpose: Prevents congestion by spacing out truck arrivals and reduces wait times.
Inbound Shipment Coordination
Use Case: A shipper/supplier coordinates with the warehouse to deliver materials just in time for production.
Purpose: Ensures efficient unloading, reduces inventory holding costs, and avoids overbooking docks.
Outbound Order Dispatching
Use Case: A warehouse schedules specific docks for order pickups by different carriers/customers.
Purpose: Helps organize outgoing shipments and maintain on-time delivery performance.
Peak Season Load Management
Use Case: During holiday seasons or promotional events, the warehouse adjusts dock schedules to handle increased volume.
Purpose: Balances workload, avoids bottlenecks, and ensures timely processing of goods.
Driver Self-Check-In and Arrival Notifications
Use Case: A driver arrives at the facility and uses the task link to check in, automatically notifying the dock manager.
Purpose: Streamlines communication, reduces manual coordination, and speeds up dock assignment and turnaround time.
How Can Arrivy Dock Scheduling Software Slash Costs?
Arrivy is a full warehouse management software specifically designed for dock appointment scheduling. Arrivy is the most flexible and integrable software you will ever find in the market. Be it scheduling with multiple calendars or managing multiple warehouses based on different locations, Arrivy Inc. does that for you. Hear it from our customers:
“Arrivy provides a ton of flexibility that allows the business owners to manage and modify the settings and setup on their own without dev work or updates from Arrivy. The scale of the things that can be changed on the fly is incredible. I’ve managed many SaaS implementations in my career, and this is hands down my favorite vendor to work with. I can’t say enough good things, and I hope to see them grow.” G2 review, (1000+ employees)
The best thing about Arrivy is that we have more than 9+ years of experience in this industry. The software itself is intuitive, optimal, and up-to-date technology, with zero downtime. Try Arrivy today.
Quick Cheat Sheet for Dock Scheduling Glossary:
– Time Slot Management is assigning trucks to a fixed arrival time to prevent dock congestion.
– Cross-docking means moving goods directly from inbound to outbound trucks without storage.
– Detention Fees are a penalty for trucks delayed beyond the agreed dock time.
– Load Planning is organizing shipments smartly to maximize truck space and efficiency.
– Trailer Spotting means pre-staging trailers in the yard for faster dock loading.
– Dynamic Dock Scheduling: Adjusting dock schedules in real-time based on unexpected changes.
– Carrier Appointment Scheduling: Scheduling and confirming truck arrival times for smoother operations.
– First-Come, First-Served (FCFS): Loading/unloading trucks in the order they arrive.
– Dock Turnaround Time: Total time a truck spends from arrival to departure.
– Yard Management System (YMS): Software to manage trailer/truck movements inside the yard.
– Dock Door Assignment: Allocating trucks to dock doors based on load needs.
– No-Show Policy: Rules and penalties for carriers missing their appointment.
– Drop and Hook: The driver swaps trailers without waiting for loading/unloading.
– Forklift: An industrial vehicle used to move and stack goods at docks.
– Just-in-Time (JIT): Receiving goods exactly when needed to reduce inventory costs.
– Palletization: Stacking goods on pallets for easier loading, moving, and storage.
– Bill of Lading (BOL): Legal document listing shipment details, required for transport.
– Lumper Service: Third-party workers hired to load or unload trucks at the dock.
– Deadhead: When a truck moves empty between loads, wasting time and fuel.
– Backhaul: Return trip cargo that prevents the truck from moving empty.
Conclusion
In summary, a well-structured dock scheduling system is your ticket to faster truck turnarounds, smoother yard traffic, and tighter cost control without the need of sacrificing customer service.
By setting clear appointment windows, keeping an eye on your core metrics (like wait times and dock utilization), and routinely fine-tuning your process, you’ll build a more efficient operation.
Final Tip: Remember to keep your carriers in the loop, invest in the right scheduling tools, and stay open to new technologies as they emerge. With these steps in place, your docks won’t just handle today’s volumes, they’ll be ready to scale and adapt as your business grows.