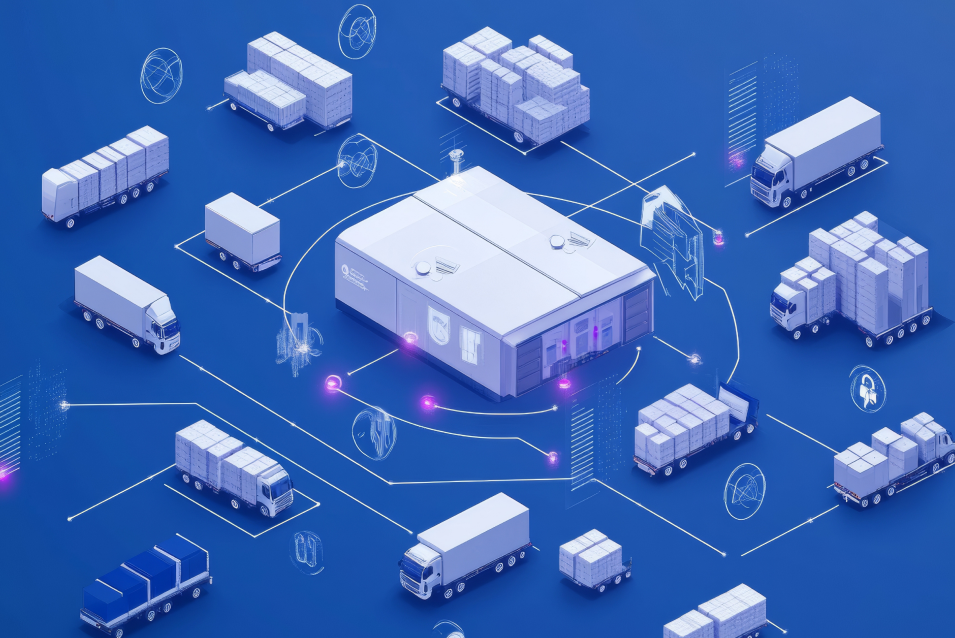
In warehouse management, one of the most daunting tasks is maintaining a smooth balance between warehouse operations and dock schedules. When handled manually, dock management is prone to time clashes, mismatched assignments, and costly delays. All of this eats into efficiency and profits.
The warehouse market is growing exponentially. An accumulative growth rate of 4.78% in the warehouse industry has been observed in the last year. Similarly, warehouse operations need to be streamlined as the surging interest in e-commerce has also been quite evident, as an increase of 8.2% is noted in 2024, closing the market at an accumulated $1.9 trillion.
Simultaneously, warehouse complexities are amplifying, customer expectations are rising, and operational bottlenecks are becoming harder to ignore. Traditional methods, including spreadsheets, phone calls, and paper logs, are no longer efficient. The decentralized approach, though familiar, slows down processes and introduces avoidable risks.
This is where a centralized logistics portal becomes indispensable. Unifying everything in one portal eliminates inefficiencies, reduces delays, and cuts unnecessary costs. A scenario-based example can help us understand the need for a centralized logistics portal and the inefficiencies of manual warehouse management.
How would it feel if it’s peak season, and your warehouse is buzzing with activity? Wonderful, right? Trucks are lining up outside, waiting hours to get an available dock. Inside, your team is scrambling, manually checking schedules, shuffling appointments, and dealing with last-minute changes because a shipment arrived earlier than expected. Meanwhile, another dock sits idle because no one realized it was free. It will be a collapse, chaos, and a lack of visibility.
Let’s make it clearer with another example.
What happens when your warehouse still relies on spreadsheets, phone calls, and sticky notes to manage dock schedules? Your team gets a call from a carrier: “We’ll arrive at 2 PM with a 20,000-lb shipment, and we need a standard dock.”
Your clerk spends 15 minutes digging through sheets to check availability. They realize Dock 5 is already booked, but Dock 8 is free. Another 10 minutes to update the spreadsheet. They call the carrier back, but the driver can’t take Dock 8 (it lacks the right equipment). 20 more minutes of back-and-forth. Finally, they rescheduled for 4 PM, delaying unloading by 2 hours.
The Result?
- $150 in detention fees (75/hour x 2 hours)
- 45 minutes of wasted labor ($30 in payroll)
- A frustrated carrier (who may charge you higher rates next time)
The Hidden Costs of Poor Dock Management
Many warehouse operators underestimate just how much inefficiency eats into their bottom line. Without a centralized logistics portal, businesses lose their money in ways that aren’t always immediately obvious.
1. Dock Congestion & Detention Fees
According to the Federal Motor Carrier Safety Administration (FMCSA), warehouses can incur carrier detention fees and penalties for loading or unloading delays, ranging from $25 to $90 per hour per truck. Manual scheduling leads to missed appointments, overtime labor spikes, and carrier penalties.
2. Misdirected Shipments
In warehouse management, every dock assignment impacts efficiency and product integrity. Manual scheduling often leads to misrouted shipments as delicate goods may get placed incorrectly, or priority orders get delayed by avoidable bottlenecks. These inefficiencies strain resources, disrupt timelines, and erode customer trust.
The practical solution is the implementation of dock scheduling software. It simplifies the scheduling process, eliminating the need to manually make calls and spreadsheets. Warehouses can mitigate errors, maximize throughput, and maximize efficiency.
3. The Domino Effect of Manual Handoffs
Paper logs and spreadsheets have higher chances of predictable failures in modern warehouses. A single scheduling error forces trucks to queue unnecessarily, while misplaced shipments require costly manual intervention.
These inefficiencies compound rapidly, affecting customer satisfaction. Such outdated methods transform simple dock assignments into recurring profit leaks across your operation.
4. Customer Trust Erodes Quickly
In an era where Amazon has conditioned consumers to expect same-day or next-day delivery, even minor delays can drive customers away. A PwC survey found that 32% of buyers abandon a brand after just one negative delivery experience. Without a centralized logistics portal, warehouses struggle to meet SLAs, leading to dissatisfied clients and lost revenue.
What is a Centralized Logistics Portal?
A Centralized logistics portal is a unified digital platform that incorporates all critical logistics operations, like dock scheduling and warehouse management, to carrier coordination and real-time analytics into a single, cloud-based command center.
Generally, the warehouses operate manually by managing spreadsheets, calling, and booking. However, dashboards passively report metrics. But this portal dynamically allocates resources, predicts hurdles, and enforces operational protocols with automation of dock allotments, scheduling, and timely arrivals.
Key Distinctions from Conventional Systems
Traditional dock scheduling solutions focus merely on specific tasks, such as tracking stock or managing shipments, but they fail to connect these functions cohesively.
Whereas a centralized portal breaks it down by:
- Providing a unified warehouse dashboard where managers see live KPIs, from order statuses to dock utilization.
- Automating warehouse scheduling to eliminate barriers, reduce detention fees, and optimize labor allocation.
- Offering role-specific access, ensuring drivers, suppliers, and customers interact with the system in the most efficient way possible.
A centrally controlled warehouse dashboard redefines dock management by providing complete control of managing multiple warehouses simultaneously. Additionally, it automatically assigns shipments to optimal bays based on load type and labor availability. Where a WMS merely tracks inventory and a TMS optimizes routes, this portal sets up the intersection of both, ensuring refrigerated freight auto-assigns to chilled docks while expedited shipments claim priority slots.
How a Centralized Logistics Portal Optimizes Multi-Dock Operations?
A centralized logistics portal is a necessity for any warehouse looking to stay competitive. Here’s how its core features dismantle inefficiencies:
1. Smart Dock Allocation Based on Type & Priority
Every dock schedule has its specifications. Here, a centralized portal accelerates the task by:
- Automatically assigns docks by category (e.g., frozen goods to temperature-controlled bays).
- Prioritizes high-urgency shipments (e.g., same-day e-commerce orders).
2. Real-Time Visibility for All Stakeholders
- Shippers: Shippers can track shipments in transit and receive automated dock assignment alerts.
- Carriers: Get mobile alerts for check-in QR codes and real-time dock availability.
- Customers: Monitor delivery status and estimated arrival times for better planning.
- Warehouses: Optimize dock utilization with live dashboards and self-scheduling for inbound shipments.
3. Cost & Time Savings Through Automation
- Reduced Detention Fees: Automated dock scheduling cut idle time by 40–50%.
- Labor Optimization: Predefined workflows free staff to focus on exceptions.
- Fewer Errors: Digital tracking eliminates misrouted shipments.
Case Study: As stated by xChange, if your container is delayed by 14 days, the average detention fee in a big city like New York can cost you a massive $2,478 per container. Even the lowest recorded fee, $548 in Hamburg, can still hit your budget. (Read More)
4. Real-Time Warehouse Dashboards
A centralized logistics portal has a warehouse dashboard where managers see live updates on dock availability. Everything aligns at the center. The need to scramble between systems or wait for manual reports gets eliminated. A warehouse dashboard provides instant visibility, allowing teams to:
- Anticipate roadblocks before they cause delays
- Track carrier ETAs to optimize dock scheduling
Who Benefits?
A centralized logistics portal isn’t a one-size tool that fits all. It’s designed to serve every user optimally.
Warehouse Managers
For managers, the portal is a lifeline. Instead of drowning in spreadsheets and phone calls, they gain:
- Real-time oversight of all operations.
- Predictive analytics to optimize staffing and inventory.
- Automated reporting for compliance and audits.
Carriers and Drivers
Drivers waste hours waiting for dock assignments or paperwork. A portal eliminates this friction by:
- Providing mobile check-in and digital instructions.
- Alerting them in real time if schedules change.
- Reducing detention time, improving their route efficiency.
Customers
In contemporary times, customers demand visibility and rely more on facts than assumptions. A portal lets them:
- Track shipments in real time.
- Access invoices and PODs digitally.
- Receive automated delay notifications.
Suppliers and Vendors
Suppliers no longer need to call for appointment slots. Instead, they:
- Book inbound deliveries via self-service.
- Receive instant confirmations.
- Get alerts for schedule changes.
Final Thoughts
Warehouses are abandoning manual and guesswork-driven processes. Warehouse velocity demands precision coordination that only centralized control provides. The portal’s mandatory status stems from its unique capacity to convert three critical operational liabilities: detention costs, labor inefficiency, and capacity waste, into measurable competitive advantages.