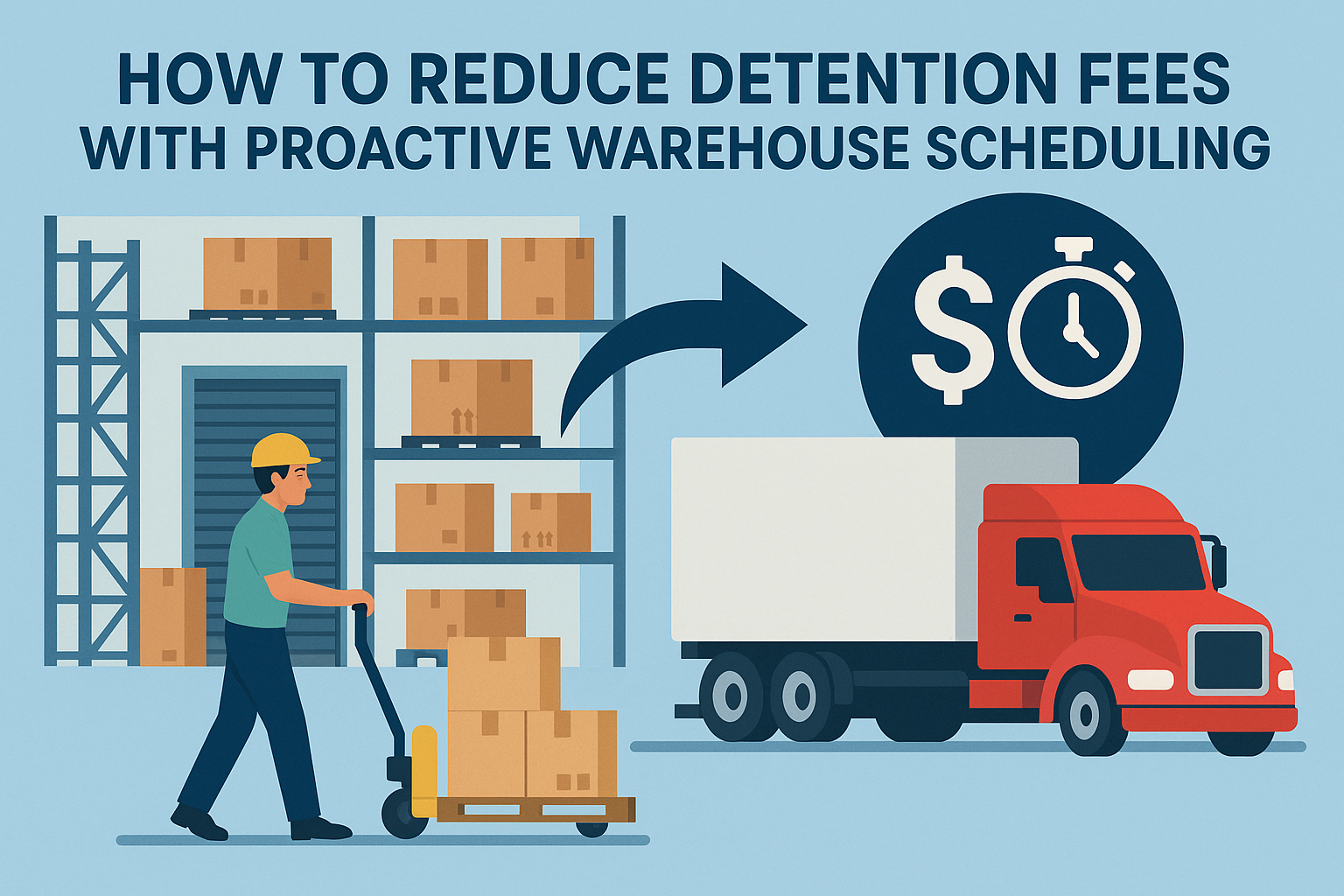
As a warehouse owner or manager, have you ever wondered why your end of the month costs sometimes include unexpected charges that are out of your allotted budget labeled as “detention fees”?. When it comes to handling shipments, one of the most common challenges warehouses face is detention fees.
So, what are detention charges?
A detention fee is a chargeback, fine, or penalty that is only incurred when you hold a truck or driver too long beyond the allotted free time for loading or unloading. In simple words, “It’s the late fees applied when you don’t return the fleet after using it“. It can ruin your logistics budget while damaging the relationships with suppliers.
What is the Cost of Detention Fees?
Any period where drivers are waiting without making any forward progress counts as a financial burden for warehouses. That’s why you need to understand what causes detention time and the costs involved. Detention fee, charged to warehouses for waiting beyond the allowed free time, can range from $25 to $100, depending on your location.
These fees rise quickly by passing hours and can lead to thousands of dollars in extra costs each week for high-volume shippers. As stated by xChange, if your container is delayed by 14 days, the average detention fee in a big city like New York can cost you a massive $2,478 per container. Even the lowest recorded fee, $548 in Hamburg, can still hit your budget.
According to the Federal Maritime Commission, the total amount of detention has increased 10-fold after the pandemic, which is 86% higher than in the past. From 2020 to 2023, the nine major carriers in the US have collected roughly $13.8 billion in detention and demurrage charges. So, it is evident that you should proactively do something to avoid these huge overhead costs that secretly impact your bottom line. First, let’s discuss what is causing it.
What are the Causes of Detention Fees?
Three problems that all warehouses, retailers, and carriers have in common are :
- Dock Congestion
- Over-worked employees
- Piles of Paperwork
For most warehouses, making sure your yard is “clean” for upcoming shipments sounds like a dream. An interesting stat from DHL discloses that the average wait time a driver has to stay is 2.5 hours, and wait for no reason in the warehouse due to inefficient operations.
For instance, the DHL team analyzed that on average, it takes 30 minutes to unload 24 pallets off a 48’ trailer, which implies that if four prior trucks are standing in line waiting to be unload, then the driver on the fifth container has to stay an extra 2 hours while waiting for others. This is such a time-consuming task, which costs a lot of money from your budget. Other than natural disasters, adverse weather conditions, and traffic issues, the causes that lead to detention fees are:
1) Lack of real-time coordination between shippers, carriers, and receivers.
2) Misunderstanding due to half- or full misinformation over the phone calls.
3) Prolonged container usage due to scheduling conflicts.
But there are solutions to each problem, right? With nearly 40% of truckloads in the US are facing detention fees, inefficient scheduling is a major contributor to these avoidable expenses.
Dock Scheduling Software: The Only Solution You Have Been Waiting for!
Imagine having a system that connects your drivers, carrier, and shipper in seamless coordination so you don’t have to stand in a warehouse dialing numbers. What if there is a way you can already predict these long wait times before they even happen? That’s exactly where Dock Scheduling software comes into play.
Proactively (before it even begins) managing your warehouse workflows, such as setting up career appointments, leads to reduced overlap and less congestion at the loading dock. So now the only question left is how it works & why it is so effective! So now the only question left is how it works & why it is so effective!
How Dock Scheduling Software Can Help Reduce Detention Fees?
A Dock Scheduling Software can book your loading and unloading times and help you with documentation. And manage dock appointments in advance. Here is what it can do:
✔ Book Dock Appointment with Calendar view: Your carriers and shippers can book their appointments by themselves, reducing double booking and overlapping schedules.
- Carriers can book in advance, no login is needed
- AI-powered system allocates resources in a balanced way.
- Individual turn-key customer portal in which carriers, shippers, and receivers can see their upcoming appointments, book more, and access digital documentation of each task.
- Set up your dock availability and buffer times, service times, and maintenance hours.
- Create booking slots based on the sizes of your truck.
For instance, Arrivy is a dock scheduling software that helps warehouses reduce overbooking and helps you cut detention fees.
✔ Coordinate Drivers and their Schedules: Imagine everyone knows about the freight, be it the shipper or warehouse teams. This way, your team knows which shipment will arrive, load, and unload first. If they coordinate the tasks effectively, teams can clean up the yard before the subsequent shipments come. By including dock scheduling, you avoid FIFO or post-mortem techniques as your software tells you what to do.
✔ Digital Paperwork: Be it purchase orders, checklists, recording arrival times, calculating wait times, or detention fees, all of this can be handled on digital paperwork within your mobile app, so you avoid using cluttered paper, which can be lost anytime. With dock scheduling software you can:
- Upload key documents easily (BOLs, POs, images, and more)
- Access & store PDF documents securely
- Easy-to-use, shareable multi-user forms
- Capture signatures digitally on the go
✔ Get your KPIs and Metrics Straight: Knowing where your operations stand and proactively measuring performance can be a hassle if done manually. When schedules and updates are handled inside software, it’s easy to track your KPIs and improve your current performance.
How to Proactively Implement Dock Scheduling Software?
Know your needs:
Before diving into the pool of software out there, list out what you want your software to do. Know what the problems are. Are you trying to reduce wait times, detention fees, improve communication, or gain operational insights? Knowing your goals can get you to the right software.
Go through multiple options:
Don’t settle for the first option you find. Take your time to go through several dock scheduling platforms according to your requirements. Look at common features that align with your problems, pricing structures, and integration capabilities with your existing systems. Reading user reviews and requesting demos can also reveal how each solution performs in real-world scenarios.
Monitor with a free trial:
Before buying or committing to full implementation processes, use free trials to verify whether the software has a practical impact. Watch closely, see if it’s easy for your team to understand and interact with, and check if it collects feedback. Examine the mobile app UI since most drivers are laypeople who need straightforward interfaces.
Benefits of Dock Scheduling Software
- Most warehouses are still stuck on spreadsheets, but dock scheduling software slashes this tiring process. All can be done on a seamless calendar view, you can reschedule and assign, and edit times whenever you want.
- Drivers are always coordinating and your team is constantly getting ETA alerts, they know when to act fast before shipment arrives, which means no detention fees, wait times or long line-ups in the full yard.
- Warehouse managers can sit in one office and manage operations for multiple warehouses, which gives visibility and coordination for all operations.
- For repeat customers, scheduling software offers personalized portal access where they can view upcoming tasks, forms, schedule appointments, and check job history, all in one convenient place to manage their schedules.
Why Does Putting Money into Dock Scheduling Software Make Sense?
Scheduling that is powered by automation and AI enables warehouses to optimize their workflows and plan loads faster while saving costs. In 2024, the costmine whitepaper reveals that 20% of shipper costs were saved after implementing dock scheduling software.
You know how quickly the cost of detention fees keeps on adding up, with the right dock scheduling software, these costs can be completely avoided, Instead it becomes an asset for companies in the long run. In order to smoothly run your operations, dock scheduling software can save money and improve driver satisfaction. So, yes a good software is worth the investment.
Final Thoughts
Scheduling a single dock appointment can take upto 15 minutes on Excel sheets. When calculated annually, it can cost days of work. Implementing dock scheduling software comes as one of the effective ways to proactively address the issues related to warehouse management, specifically detention and demurrage fee.
The implication of detention fees might be a pushover to make warehouses more efficient, but it impacts your bottom line. If your warehouse operations are struggling with a pinch of detention fees that hurts your revenue, it’s time to include appointment scheduling software in your operations.
At Arrivy dock scheduling platform, we understand the needs of each user; we craft tailored plans and help teams deal with on-time execution through multiple features. Get a 1-1 30-minute free consultation and 14-day free trial to measure the impact. Arrivy is simple and intuitive to use. Book a free demo to learn more.