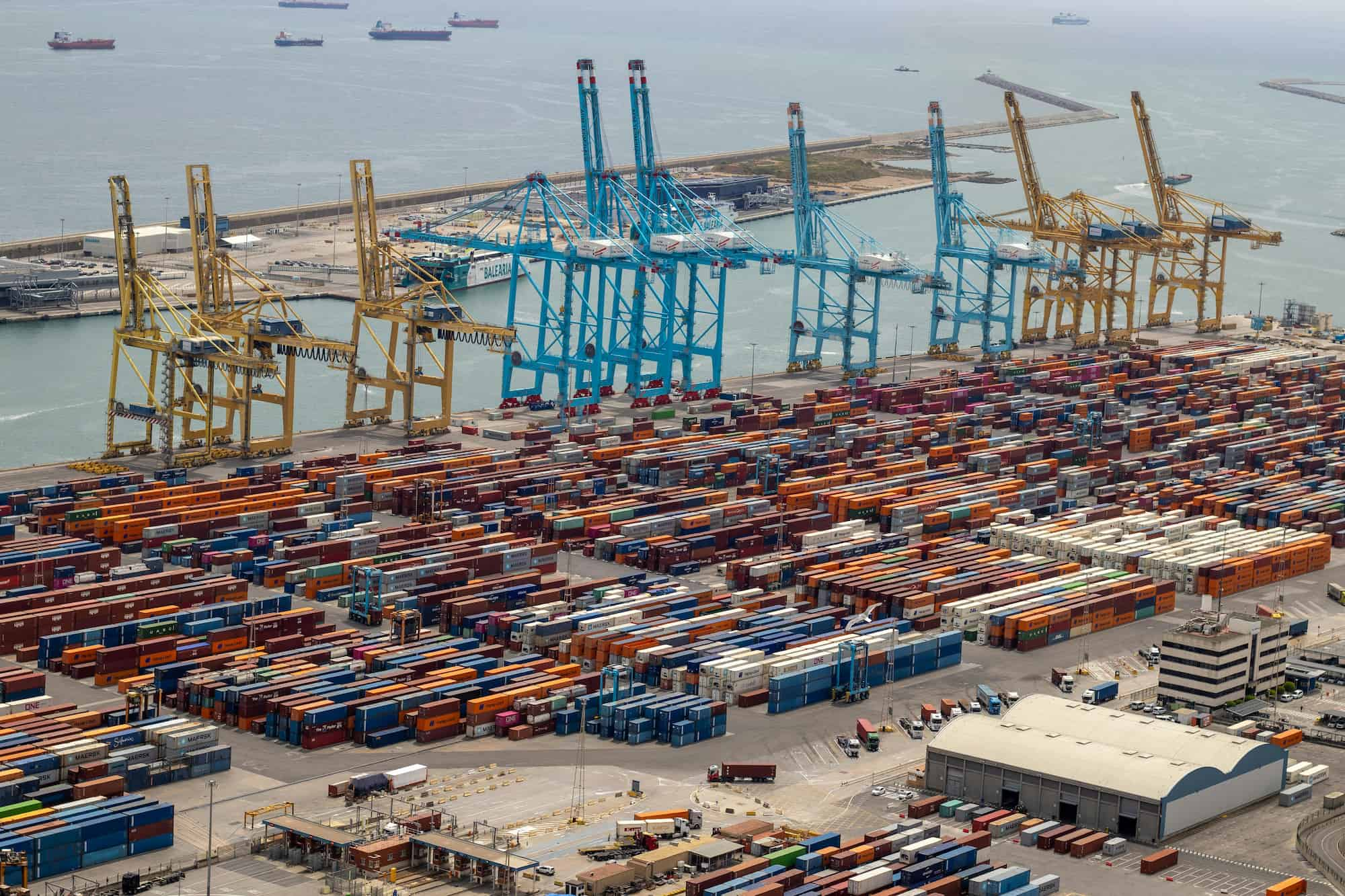
In the fast-moving world of logistics and warehousing, every minute counts. Managing truck arrivals, coordinating with carriers, minimizing dock congestion, and enhancing visibility are essential for operational success. This is where dock scheduling software becomes a game-changer.
“Efficient dock scheduling isn’t just a convenience, it’s the backbone of a responsive, resilient supply chain.”
— Michael Zimmerman, Partner at Kearney and Lead of the Global Logistics Practice
What Is Dock Scheduling Software?
Let’s be real, warehouse chaos is no myth. Between surprise truck arrivals, delayed shipments, and misaligned schedules, managing docks can feel like herding cats. Logistics coordinators often share stories of two carriers showing up for the same dock slot, causing backups that take hours to untangle. That’s where dock scheduling software proves its worth. It replaces guesswork with precision, giving your team the tools to plan smarter, move faster, and keep operations flowing like clockwork.
Quick Benefits
- Reduced dock congestion and detention fees
- Streamlined communication between carriers, suppliers, and internal teams
- Increased visibility into daily operations
- Better use of warehouse resources and staff
- Fewer scheduling conflicts and missed appointments
Feature-Driven Solutions: Solving Real Dock Challenges
Each feature of modern dock scheduling software targets a specific pain point in traditional warehouse operations. Let’s explore how:
1. Carrier Self-Scheduling
Warehouse managers often lose valuable time coordinating with carriers over calls and emails, resulting in operational inefficiencies and costly detention fees. According to the Federal Motor Carrier Safety Administration (FMCSA), warehouses can incur carrier detention fees and penalties for loading or unloading delays, ranging from $25 to $90 per hour per truck.
Carrier Self-Scheduling empowers carriers to book, reschedule, or cancel their own appointments through a secure and centralized portal. This feature allows them to view real-time availability of loading docks and choose the time slots that align with their schedules without needing to contact warehouse personnel directly.
2. Automated Scheduling & Notifications
Manual scheduling often leads to errors, missed appointments, and dock congestion. Dock Scheduling Software eliminates these issues by automating appointments using predefined rules and conditions for better accuracy.
It also sends real-time updates to carriers and warehouse staff about schedule changes or delays. This automation boosts reliability, significantly reduces no-shows, and keeps your dock operations running smoothly with minimal manual effort.
3. Advanced Time-Slot Configuration
Not all trucks or deliveries are created equal, yet many systems treat them the same. Dock Scheduling software allows creation of dynamic slots based on multiple factors such as truck type, number of pallets, or product category. You can even customize slots based on unloading time, equipment availability, or carrier priority, ensuring accurate and efficient scheduling. A dock scheduling software can reduce average truck wait times by 30–50%, improving overall throughput.
4. Multiple and Easy Calendar Views
Dock Scheduling software provides intuitive and flexible calendar views that make dock scheduling simple and enhance visibility. Whether you need a daily, weekly, or monthly layout, calendars adjust to your workflow.
You can easily view, filter, and manage bookings across multiple docks, carriers, or shifts in one centralized view. With color-coded time slots and drag-and-drop functionality, tracking and adjusting schedules becomes efficient, helping teams stay organized and avoid scheduling conflicts or congestion.
5. Real-Time Visibility & Scheduling
When real-time updates are missing, warehouse teams are caught off guard by delays or changes. Dock Scheduling software offers live dashboards that clearly display scheduled appointments, arrivals, and any unexpected delays. You can track all dock activity in one place and adjust schedules or staff allocation as required. Over 60% of logistics firms consider real-time visibility and live dashboards as essential for modern warehousing operations.
6. Scalability & Customization
As warehouse operations grow, many scheduling systems struggle to keep up, leading to operational bottlenecks and inefficiencies. Most legacy tools were not designed with expansion in mind, and quickly become outdated as your supplier network or number of locations increases. That’s where Dock Scheduling software stands out. Whether you’re managing a single dock or overseeing hundreds across multiple geographic locations, Arrivy is built to scale with your business.
7. Multi-Dock/Warehouse Management
When you’re handling operations across multiple docks, shifts, or warehouse locations, things can get messy fast. Manually toggling between separate systems or tools for each site often leads to scheduling conflicts, delays, and lack of real-time oversight. In a study last year, 63% of the truck drivers claimed that they waited for 3 hours every time at the shipping dock.
Dock Scheduling software solves this chaos with its robust multi-dock and warehouse management capabilities. The platform gives you a centralized dashboard where you can easily switch between locations, manage bookings, and enforce location-specific rules and workflows. Whether it’s assigning time slots based on the type of delivery, prioritizing certain docks for high-volume shipments, or enforcing different unloading protocols at each facility, Dock Scheduling software gives you the flexibility and control to manage it all from one unified system.
8. Reporting & Analytics
Manual dock scheduling might keep the wheels turning, but it rarely provides the insights needed to make data-driven decisions. Without visibility into performance metrics, inefficiencies often go unnoticed until they snowball into major operational issues. That’s why Dock Scheduling software integrates comprehensive reporting and analytics tools directly into its platform. These analytics give you a clear picture of what’s working and where improvements are needed.
Manual vs. Automated Dock Scheduling: A Side-by-Side Comparison
Manual dock scheduling may have worked in the past, but today’s complex logistics landscape demands speed, precision, and adaptability. Here’s how automated dock scheduling software outperforms manual methods across the board:
Time Efficiency
Manual: Hours wasted on back-and-forth phone calls and emails to book, reschedule, or cancel appointments.
Automated: Digital portals enable instant scheduling, rescheduling, and cancellations—no human bottlenecks.
Scheduling Accuracy
Manual: Prone to double bookings, scheduling conflicts, and missed appointments due to human error.
Automated: Built-in conflict detection, smart rescheduling rules, and dynamic slot management ensure smooth operations.
Visibility
Manual: Limited to whiteboards, spreadsheets, or isolated documents, leading to poor oversight.
Automated: Real-time dashboards display live dock activity, arrivals, and delays across all locations.
Scalability
Manual: Difficult to scale across multiple docks, shifts, or warehouses. Processes break down as volume grows.
Automated: Easily manages hundreds of docks or locations within a single centralized system, built to scale with your business.
Error Reduction
Manual: High risk of human errors, from overbooking to missed updates.
Automated: Automation and logic-based scheduling drastically reduce error rates and improve consistency.
Reporting & Analytics
Manual: Often lacks structured data collection—reports are inconsistent or missing entirely.
Automated: Generates detailed performance reports, KPIs, and historical data to support continuous improvement.
Customer & Carrier Experience
Manual: Inconsistent communication, delayed updates, and frustration for carriers.
Automated: Self-service portals, real-time updates, and smooth coordination deliver a better experience for all parties.
Conclusion
In today’s competitive logistics and warehousing landscape, relying on manual dock scheduling methods is no longer a viable option. From reducing congestion and delays to enhancing communication and visibility, dock scheduling software like Arrivy provides a comprehensive, scalable solution that addresses the real challenges warehouses encounter every day. With intelligent automation, real-time tracking, and powerful customization options, it helps empower businesses to streamline operations, minimize errors, and deliver a superior experience to both carriers and customers. Choosing the right dock scheduling software is not just about convenience—it’s about future-proofing your logistics strategy.