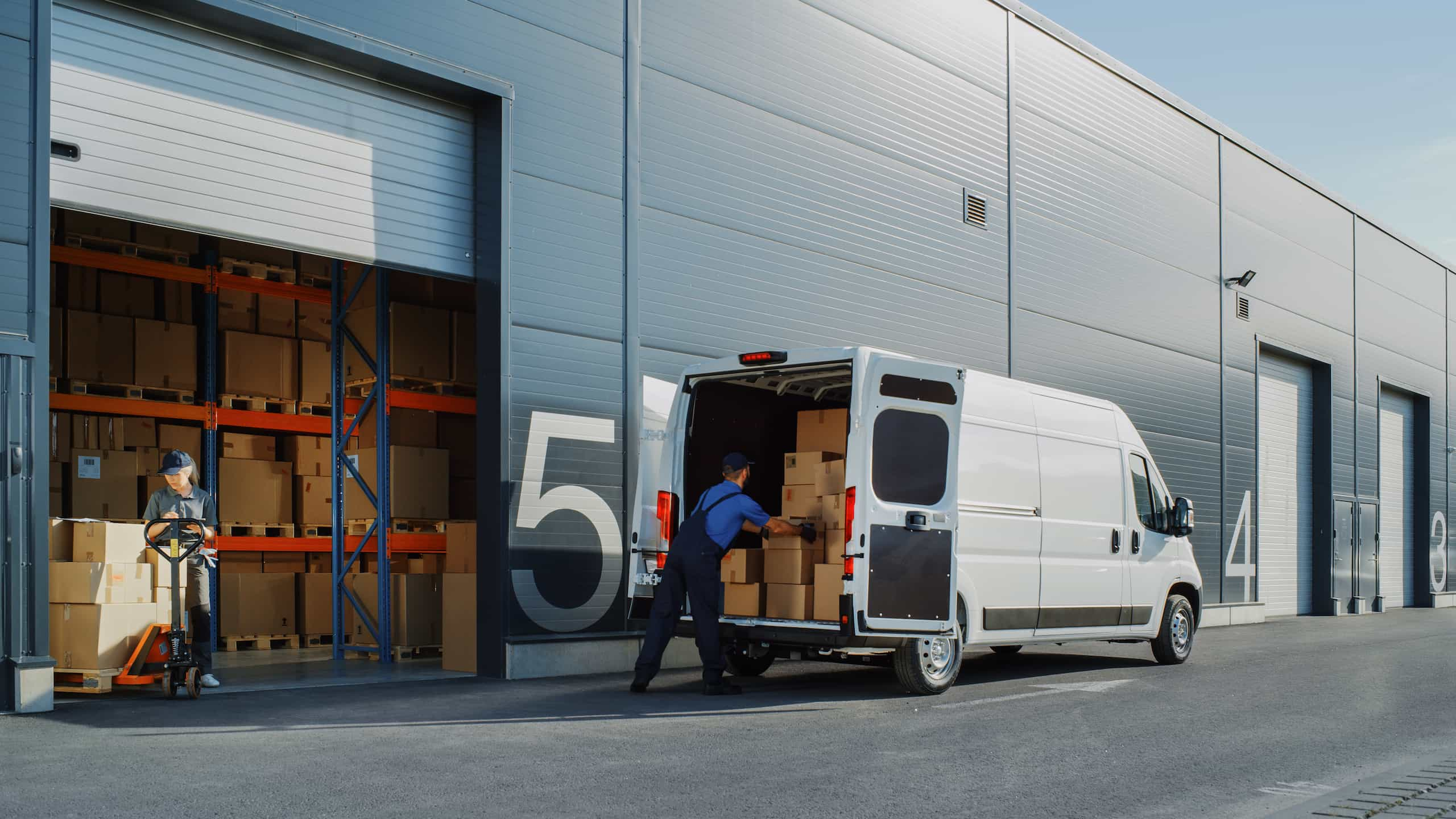
Managing pharmaceutical distribution means following strict standards set by bodies such as the FDA (U.S.) and the EMA (Europe), alongside frameworks like Good Distribution Practices (GDP).
These are the guidelines that govern how medications must be stored, managed, and moved to keep patients safe.
Failure to comply with these established rules can trigger severe penalties for pharmaceutical warehouses, encompassing significant financial burdens, revocation of operational permits, reputational harm, and, critically, endangering the lives of individuals.
This blog explores how effective dock scheduling helps pharmaceutical facilities stay compliant and avoid costly setbacks.
The Dockside Problem Most Pharma Teams Miss
Pharmaceutical logistics involves multiple handoffs, but few are as vulnerable as the loading and unloading stage of drugs is a period of heightened risk. It’s the point where custody shifts, conditions can fluctuate, and mistakes, if unnoticed, can quietly compromise compliance. That’s why as per the National Library of Medicine, up to 50% of vaccines, as much as half annually, are compromised due to mishandling during the transit of drugs. Consequently, one of the most vital areas for compliance is the loading dock, where control of goods transfers from one entity to another. It’s also where the risk of temperature loss, contamination, or theft is highest.
To illustrate, cold chain products like vaccines must stay within a specific temperature range; even a small lapse can render an entire consignment unusable. As per IQVIA, cold chain issues cost approximately $35 billion annually.
Similarly, high-value drugs or controlled substances must be protected from illicit access or fake alteration because these risks can lead to harm to the potential end user.
To meet these strict standards, companies need strong processes at the dock, such as:
- Separating different types of products
- Keeping detailed records of every transfer.
- Having real-time monitoring
Furthermore, these comprehensive records of compliance at the dock also serve as verifiable evidence of regulatory compliance when facilities are routinely audited by compliance officers.
Why Dock Scheduling Is Critical for Compliance?
Considering that a majority of regulatory and quality failures arise from a handful of essential process deficiencies, it is important to grasp how the dock scheduling interface directly tackles these weaknesses.
The Dock Scheduling Software helps compliance Managers gain the tools they need to fulfill their primary responsibilities first.
This simplifies the process of adhering to regulations and simultaneously boosts operational efficiency. Here’s how the dock directly handles it all:
1. Prevents Temperature Excursions (GDP Compliance Risk)
If a refrigerated truck sits too long waiting for a dock door to open, the internal temperature can rise past the 2-8°C threshold, ruining the shipment.
Almost 1 in 3 pharma shipments face deviations (IQVIA), often due to poor dock planning.
Scheduled appointments through dock Scheduling Software can minimize dwell time, keeping shipments within compliance.
2. Reduces Audit Failures
High-risk biologics always need priority docks. Without scheduling, sensitive products may end up at docks with no temperature monitoring or trained staff.
Random unloading of unscheduled shipments also leads to missed checklists, improper handling, and failed audits. Slotting by risk level ensures compliant unloading.
3. Eliminates Congestion (Missed SLAs & Penalties)
There can be two scenarios without scheduling: one being that trucks stack up one upon the other on the dock, and the second being that delayed shipments lead to rushed inspections, missed SLAs, and overtime labor costs.
Lack of planning in a facility without knowing shipment volumes in advance, warehouses are understaffed or misallocated resources.
The solution lies in centralized dock appointment booking, which smooths workflow, ensuring staff and docks are ready before the shipments come.
Potential Risks without proper scheduling:
- Temperature excursions (failed shipments)
- Audit findings (improper handling)
- Costly delays (congestion & labor inefficiency)
A ParkourSC survey found that 90% of pharma manufacturers and distributors lacked full in-transit visibility and did not trust the data they were receiving.
How Does Dock Scheduling Software Empower Compliance in Pharmaceutical Logistics?
Dock scheduling helps pharma facilities stay compliant. Here are five essential functions that support GxP guidelines, protect product quality, and ensure full traceability.
1. Optimized Appointment Slots
Dynamic, time-slot-based booking is a scheduling method that allocates dock access based on load type, priority, and availability, which helps prevent congestion and preserve cold chain integrity.
Logistical inefficiencies, such as unorganized truck queues and overscheduled loading bays, can introduce several operational hazards, including:
- Cold chain breaks as trailers sit too long
- Inspections rushed, SOPs missed
- Not enough staff for sensitive shipments
With scheduling software:
- You control who arrives when, how often, and with what load type.
- Carriers book pre-approved slots based on your warehouse’s actual capacity and staff availability.
- You maintain control over dwell times, reducing delays and mismanagement.
This gives you and your team timely, controlled dock operations with no unplanned exposure risks.
2. Load-Type Prioritization
The world of shipping has a diverse landscape, and this is acutely evident in the pharmaceutical sector.
The requirements are highly specific: consider biologics, hazardous materials, and cancer therapies. Every one of these deliveries demands a thoroughly prepared loading dock. This preparation needs to be validated and documented in order to stay compliant with every applicable rule.
By using dock scheduling software:
- Loads are automatically routed to the right dock based on their classification (cold chain, sterile, hazardous, etc.).
- Only validated carriers and pre-qualified suppliers can book those slots through the customer portal.
Our customers here at Arrivy have given their carriers and shippers a personalized portal with their unique credentials, through which only contracted and validated shippers can send consignments to your facility.
- Dock areas can be pre-conditioned ahead of time to meet environmental needs through pre-arrival coordination.
Example: For cold-sensitive APIs, Arrivy can trigger alerts once the truck reaches the facility gate, so the teams are notified, so they can pre-cool the dock to GDP specs.
3. Real-Time Visibility & Alerts
Your compliance must be only as strong as your visibility.
Traditional logistics relies on calls and spreadsheets. In pharma, that won’t cut it. If a temperature-sensitive shipment is running late or stuck in traffic, you need to respond now, not after it’s spoiled.
With real-time dock scheduling:
- Docks can be reassigned or crews rescheduled through prompt alerts on their tablets or phones.
This way, you protect cold chain windows, avoid compliance gaps, and reduce emergency rejections.
4. Digital Checklists & SOPs
Paper logs and verbal or phone instructions create risk, and regulators know it.
Many recalls each year stem from labeling and packaging issues alone. That’s before we even talk about handling, hygiene, or seal verification.
With dock scheduling software:
- Every load triggers a tailored checklist based on its compliance category.
- Your dock crew is prompted to check:
- Temperature logs
- Tamper seal integrity
- Vehicle sanitization
- Label verification (serialization, batch numbers, expiry)
- Digital sign-offs tie every step to a specific user, with time stamps for traceability.
This ensures compliance with 21 CFR Part 11 and GDP/GMP protocols automatically.
By deploying checklists, you build a defensible, repeatable dock process that stands up to any audit without any missed steps.
5. Chain-of-Custody Control
From API arrival to finished product shipment, every handoff must be traceable in pharma.
Every inbound shipment should carry a complete digital footprint: who checked it in, which dock handled it, when it arrived, and how long it dwelled, along with a record of all shared documents and whether standard operating procedures (SOPs) were followed.
This level of traceability not only strengthens compliance but also ensures accountability at every stage of the receiving process.
Dock scheduling tools can help you create a complete audit trail, capturing:
- Carrier identity
- Load classification
- Gate entry logs
- Inspection results
- Load-to-dock assignment
- Departure time
All this data is securely stored and can be exported in PDF, Excel, or via API for FDA, EMA, or ISO inspections.
Bonus Optimization: Sensitive documents (SOPs, calibration logs, batch records) can be role-restricted and automatically attached to each appointment, making compliance part of the task, not an afterthought.
Here’s what efficient dock scheduling delivers across your supply chain:
Ensures GxP Compliance During Handoffs:
Compliance isn’t something you check afterward; it’s built into the process. Scheduling creates a predictable, documentable chain of custody and quality control at every step.
Maintains Product Integrity
By eliminating idle time and automating environmental checks, dock scheduling helps preserve the cold chain and prevent contamination.
Boosts Throughput Without Cutting Corners
Smart scheduling reduces wait times, improves dock utilization, and enables warehouse teams to process more loads without burnout.
Improves Carrier Coordination
No more “first come, first served.” Carriers get visibility into dock availability and ETAs, and you avoid surprises at the gate.
Fewer Missed Windows, Fewer Excursions
With real-time alerts, you prevent high-risk freight from sitting in a trailer too long. You also gain time to reroute delayed loads before they become unusable.
Arrivy’s Role in Enabling Pharma Dock Optimization
At Arrivy, we’ve helped regulated facilities build dock workflows that don’t just reduce delays, they make audits easier, reduce spoilage, and improve crew productivity.
Our dynamic scheduling system allows:
- Supplier self-booking with validation control
- Automated dock and crew assignments
- Live dashboards for supervisors and QA teams
- Role-based SOP visibility
- Audit trail documentation, exportable for regulators
By integrating dock scheduling into your quality systems, you shift from reaction to prevention, and from compliance risk to compliance strength.
Why Dock Scheduling Is a Compliance Power Tool
In pharmaceutical logistics, visibility is compliance. That’s why digital tools like Arrivy’s Dock Scheduling Platform have become essential.
From real-time monitoring and secure gate entries to temperature-based slotting and audit-ready documentation, Arrivy ensures compliance is embedded into operations, not added as an afterthought.
Want to see how Arrivy can help? Book a free demo to see.
Frequently Asked Questions
In pharmaceutical logistics, no single strategy (like JIT, Cross-docking, or traditional warehousing) fits all use cases. Instead, pharmaceutical companies often adopt a hybrid model, combining elements of multiple strategies, depending on the product type, risk, regulatory requirements, and geography.)
For Example:
- Use JIT for packaging materials
- Use warehousing for biologics under the cold chain
- Use cross-docking for high-volume generics
While dock scheduling software doesn’t directly detect counterfeit drugs, it plays a critical role in preventing their entry by enforcing strict controls such as QR authentication of incoming drivers, documentation & authorization letters on their phones at one of the most vulnerable points in the supply chain while entering the facility.
Centralized scheduling (keeping carriers, shippers, and facilities connected) with load-based slotting spreads traffic evenly across shifts, ensuring temperature-sensitive shipments aren’t delayed or exposed during peak hours.
Dock scheduling software allows templated digital forms and checklists to be attached to each task, ensuring SOPs are followed. Teams can control who can view, edit, or share these forms, export them as PDFs, and store them in the cloud or within the task. This creates a clear, traceable record for audits.