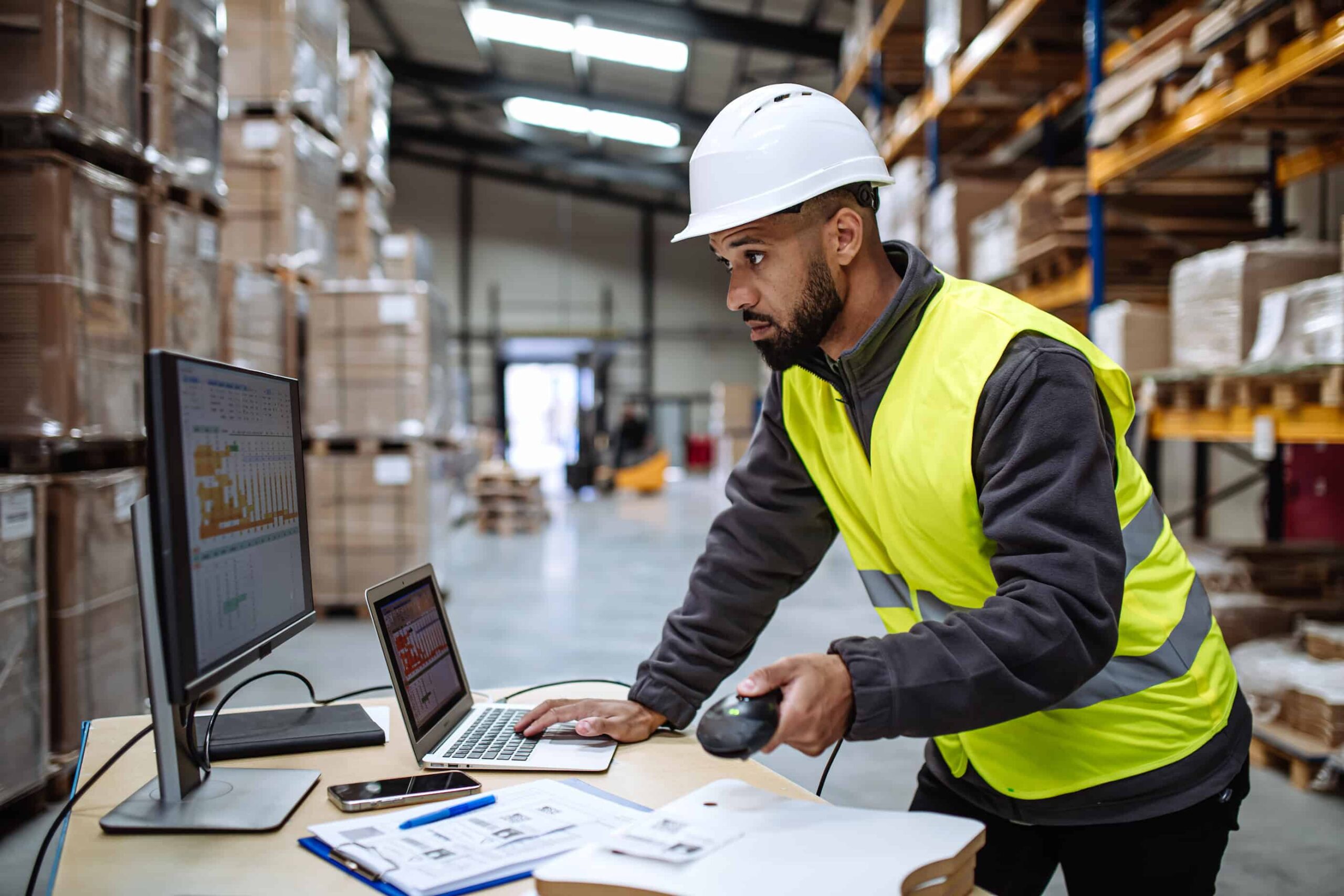
When one segment of your warehouse isn’t working right, everything else starts to feel it, and those issues can quickly propagate into systemic delays.
These are time leaks: Time leaks in warehouse management refer to small, unnoticed inefficiencies. They don’t typically show up as catastrophic failures, but when compounded, they lead to measurable declines in throughput, accuracy, and cost performance.
Over the past year, our team at Arrivy has worked closely with warehouse managers to resolve dock scheduling roadblocks across facilities of all sizes. In this blog, we’ll walk you through some of the most common sources of time leaks, how to diagnose them, and practical ways to eliminate them using tools, layout improvements, and process discipline. So, let’s get into this.
7 Common Time Leaks and How to Spot Them
1. Congested Capacity
Operating near or beyond capacity doesn’t mean you’re efficient; it usually means you’re constrained. Warehouses perform best at up to 90–95% occupancy. Beyond that, due to capacity congestion, staging areas shrink, travel paths become narrow, and simple tasks like putaway or retrieval slow down dramatically. To identify time leaks, here’s what to see:
What to check:
- Are aisles clear and staging zones functional?
- Are you relying on off-site storage or temporary overflow?
- Are inbound pallets delayed due to a lack of putaway space?
2. Underutilized Space
Not every warehouse suffers from congestion; some face the opposite issue, which is underutilization. Operating well below capacity may seem safe, but it’s often a silent drain on profitability. When it comes to wasted storage industry data shows that U.S. warehouses average only 70–80% occupancy, leaving 20–30% of the space unused. To give you a rough estimate, that’s about 4 billion square feet nationwide, translating up to $20 billion annually in wasted rent and overhead. The causes might seem very small, but their impact is quite significant. The space might be sitting idle due to:
- Ineffective putaway
- Obsolete stock occupies
- A poor slotting layout that wastes prime storage locations on slow-moving items.
- Empty or misconfigured racks are failing to utilize vertical and horizontal space efficiently.
Industrial rents have also increased to $8.31 in 2024 alone. To put this into calculation, a warehouse with 50,000 sq ft, if it sits 30% idle (unutilized), loses approximately $124,650 per year.
To identify underutilization:
What to check:
- Are warehouse entire zones or racks sitting empty for long periods?
- Is your layout optimized for flow, or is prime space wasted on low-movers?
- Can my facility support more volume before needing expansion?
By critically questioning your space, identifying layout inefficiencies that often go unnoticed can give you an idea of which places need optimization, such as reconfiguring pallet zones or utilizing upper-level racking more effectively, which can significantly increase usable capacity. These targeted adjustments not only delay the need for costly warehouse expansion but also drive better space ROI.
3. Inefficient Picking Paths & Poor Slotting
Retrieving items from storage locations to fulfill customer orders is referred to as picking. This is often the most costly and labor-intensive warehouse activity. Because this involves labor and with human-centric involvement, errors are inevitable, such as sending the wrong items or incorrect quantities. Product slotting, especially when fast-movers are buried deep in the warehouse, forces workers to walk longer paths for high-frequency SKUs, which reduces productivity and eats up their time. This happens because:
- Poor layout results in pickers traversing long distances or crisscrossing aisles
- Paper pick lists are slow, prone to errors, and require manual data entry, plus pickers have to return to a central office for new assignments.
Fixing slotting issues alone often boosts productivity up to 15–20%.
What to check:
- Are A/B/C items slotted based on frequency?
- Do pickers walk unnecessarily long routes (note down their time)?
- Are fast-moving items close to packing or dispatch zones?
Fixing Strategy
Batch Picking: Pick products for multiple orders at once, then consolidate all of them at the end of the aisle, and then put them all in one on the outbound staging areas. This reduces travel, especially for single-line orders.
Perform ABC Analysis and Slotting: Analyze stock movement (velocity) and product characteristics to place fast-moving items in easily accessible locations nearest dispatch, and items frequently shipped together next to each other. This reduces picker travel time significantly
Optimize Pick Routes: Sequence pick instructions to guide pickers along the most efficient path, minimizing backtracking and ending near the dispatch area.
4. Slow Receiving and Putaway Cycles
When inbound stock lingers on the dock or in staging zones, it blocks space and delays its availability for picking. Best-in-class organizations typically store their stock for 2 hours, while others store it for 24 hours. On the other hand, top-performing 3PLs have an average of 8–10 hours to complete dock-to-stock. To check these issues, you need to:
Look for:
- Long dock-to-stock cycles (Analyze their time through status tracking)
- Bottlenecks in putaway due to unclear storage locations
- Receiving zones that are becoming temporary warehouses
Fixing Strategy
Use Dock Scheduling Software to align labor with arrivals:
- Set up time-slot-based booking for carriers
- Limit the number of trucks that can arrive per slot to prevent overcrowding.
- View all upcoming arrivals in a real-time dashboard, categorized by dock and time.
- In order to analyze the dock-to-stock cycle, use status tracking for docks to know how much time a single dock takes to be transferred to the picking area.
For example, A truck is scheduled via Arrivy to arrive at Dock 3 at 9:00 AM. The system automatically assigns a crew of two based on availability, sends a notification at 8:30 AM, and updates the supervisor’s dashboard. Upon arrival, unloading begins immediately without congestion. If the truck is late, the crew is notified, and the dock is reassigned to a task in another zone for that window.
Additionally, automate unloading and scanning processes using conveyors, RFID, or barcode systems.
Implement WMS-guided put-away to minimize search and travel time.
5. Excess Labor Travel & Rework
Labor is your biggest asset, and often the biggest source of wasted time if processes aren’t streamlined. If employees spend time rechecking inventory, wandering for tools, or revisiting areas due to poor slotting or unclear priorities, you’re losing productivity by the minute.
Lack of synchronization between picking completion, staging, and vehicle arrivals/departures, leading to dock congestion
Ways to monitor:
- Frequent rework or order corrections
- High walking times or idle movement between picks
- Lack of mobile task visibility or real-time job assignments
Coordinated Dock Scheduling: Manage vehicle arrivals and departures precisely to align with despatch activities and available resources at loading bays, avoiding congestion
6. Declining KPIs Without Obvious Cause
If your cost-per-order, order cycle time, or pick rates are dropping, without a volume spike or labor change, it’s likely due to hidden inefficiencies.
Use KPIs to track:
- Average pick rate per person/hour
- Inbound putaway time
- Pick-to-ship time
- Order accuracy rate
If you don’t have real-time KPI dashboards, you may be flying blind and letting time leaks go undetected. Use Arrivy scheduling to have complete visibility into your warehouse operations. We can help you build your custom KPI’s and will be there for you until to get the results you desire.
7. Not Listening to the Floor
Sometimes the clearest signals come from the people closest to the process. Workers often know exactly what slows them down, whether it’s outdated layouts, bad shelf labeling, or the unavailability of picking carts.
Create structured feedback loops, surveys, short daily huddles, or suggestion logs to capture and act on what the floor already knows.
Use a Diagnostic Checklist
Arrivy recommends using a Warehouse Diagnostic Checklist monthly to catch early signs of inefficiency. Here are a few high-impact checkpoints:
- Is inventory accuracy above 98%?
- Is the pick rate aligned with industry benchmarks?
- Are pickers traveling more than necessary?
- Are inbound goods stored within 24 hours?
- Is off-site storage being used unnecessarily?
General Time Leaks: Waste in Warehousing (MUDA)
It is essential to understand the concept of “waste” (muda) as defined in lean management, which refers to any activity or process that uses resources but adds no value to the customer. Each type of Muda introduces tiny inefficiencies that may seem harmless in isolation. But across hundreds or thousands of operations per day, these time leaks snowball, affecting everything
There are seven wastes (Muda) in Warehouse Operation:
Transportation: Moving items more than necessary, such as driving an empty forklift.
Defects: Time spent correcting errors like mis-picks.
Inventories: Congestion at inbound and outbound areas due to excess stock.
Motion: Unnecessary movement, like staging a product before put-away.
Waiting Time: Roadblocks at pickup locations or equipment idle time.
Overproduction: Holding more inventory than needed.
Overprocessing: Performing unnecessary steps, such as excessive labelling or checking.
To eliminate these time leaks, experts recommend using the 5S concept (Sort, Straighten, Shine, Standardize, Sustain), a foundational lean thinking methodology that can be easily applied to the warehouse to eliminate waste and improve organization.
Sort: Remove unnecessary items like obsolete stock or damaged tools to declutter work areas.
Straighten: Organize tools and inventory so that frequently used items are easy to find and access.
Shine: Clean regularly to maintain a tidy, safe, and efficient workspace.
Standardize: Create clear, consistent procedures to ensure every task is done the best way, every time.
Sustain: Maintain improvements through regular audits and a culture of continuous improvement.
Final Thoughts
Most of the time, leaks aren’t obvious; they hide in workflows, layouts, and decision delays. But when you start measuring, observing, and adjusting, the gains are substantial.
At Arrivy, we help warehouse teams identify, fix, and prevent operational bottlenecks—from slotting strategy to digital WMS workflows. Start small: map pick paths, listen to your team, and track the right KPIs. The time savings will follow.